Understanding COGS in the CPG Industry
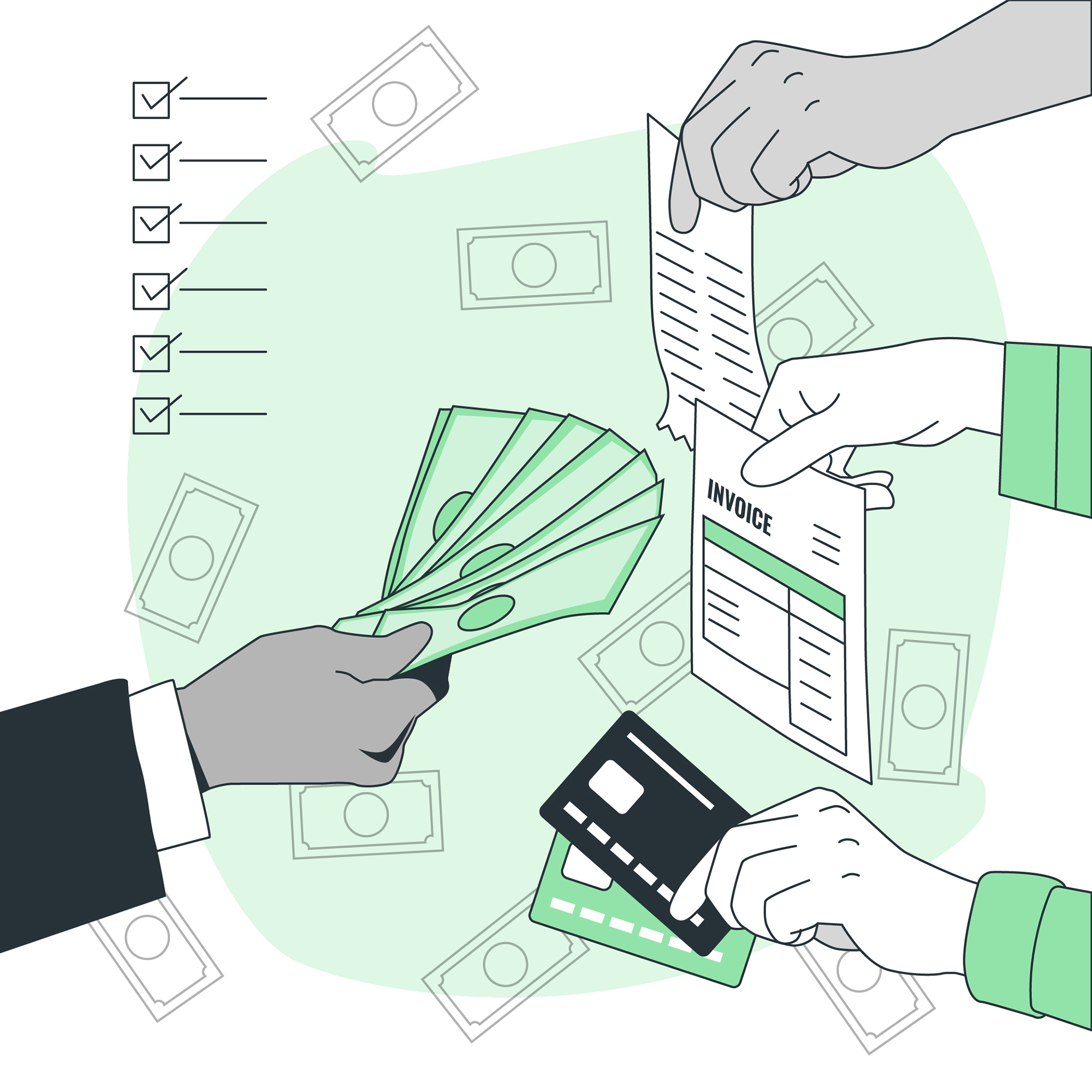
Introduction
Cost of Goods Sold (COGS) is a critical metric in the Consumer Packaged Goods (CPG) industry, representing the direct costs attributable to the production of the goods sold by a company. This includes costs related to materials, labor, and manufacturing overhead. Understanding COGS is essential for managing profitability and pricing strategies.
Components of COGS
Raw Materials
The cost of raw materials is a significant portion of COGS. This includes the price of ingredients or components that go into the final product. For instance, in a beverage company, this would cover the cost of water, flavorings, and packaging materials.
Direct Labor
Direct labor costs encompass wages for employees directly involved in production. This includes workers on the assembly line, machine operators, and quality control personnel. Efficient labor management can significantly impact COGS.
Manufacturing Overhead
Manufacturing overhead includes indirect costs associated with production, such as utilities, maintenance, and factory rent. These costs are allocated to products based on a predetermined rate and can fluctuate with changes in production volume.
Importance of COGS in the CPG Industry
Pricing Strategy
Understanding COGS helps companies set pricing strategies that ensure profitability. By accurately calculating COGS, businesses can determine the minimum price at which products can be sold without incurring losses.
Profit Margin Analysis
COGS directly affects the gross profit margin, a key indicator of financial health. By analyzing the relationship between COGS and sales revenue, companies can make informed decisions about cost management and pricing adjustments.
Inventory Management
Efficient inventory management is crucial for controlling COGS. Overstocking leads to higher storage costs and potential waste, while understocking can result in lost sales and production delays. Balancing inventory levels helps optimize COGS.
Strategies to Optimize COGS
Supplier Negotiations
Building strong relationships with suppliers and negotiating favorable terms can reduce raw material costs. Volume discounts and long-term contracts can also help manage COGS more effectively.
Process Improvement
Investing in process improvements and automation can enhance production efficiency, reducing labor and overhead costs. Lean manufacturing techniques and continuous improvement initiatives are valuable strategies in this regard.
Waste Reduction
Implementing waste reduction programs minimizes the cost of discarded materials and inefficiencies. Sustainable practices not only reduce COGS but also improve the company's environmental footprint.
Conclusion
In the CPG industry, managing COGS is essential for maintaining profitability and competitive pricing. By understanding the components of COGS and implementing strategies to optimize these costs, businesses can achieve better financial performance and operational efficiency.
Amsterdam Data Labs offers advanced analytics solutions to help CPG companies manage and optimize their COGS. Contact us today to learn how we can support your business in achieving cost efficiency and profitability.